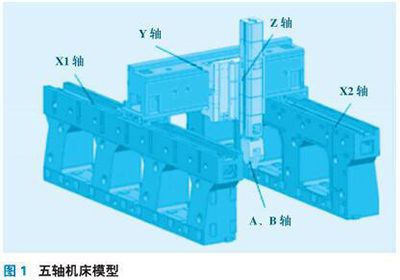
New algorithm for error modeling and compensation analysis of five-axis machine tools
Global competition forces manufacturing companies to pay more and more attention to product processing efficiency and accuracy. Product accuracy is largely determined by the accuracy of machine tools. Five-axis CNC machine tools can
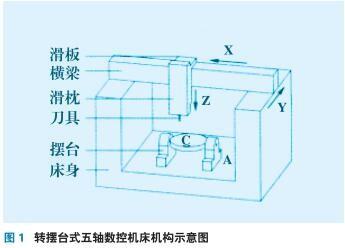
Geometric error detection and compensation of five-axis CNC machine tool rotary center
Five-axis CNC machine tools are the most important processing equipment in the equipment manufacturing industry. They can be used to process various complex curved surfaces. With the continuous improvement of workpiece processing quality requirements, how to improve the processing accuracy of five-axis CNC machine tools has become a hot topic.
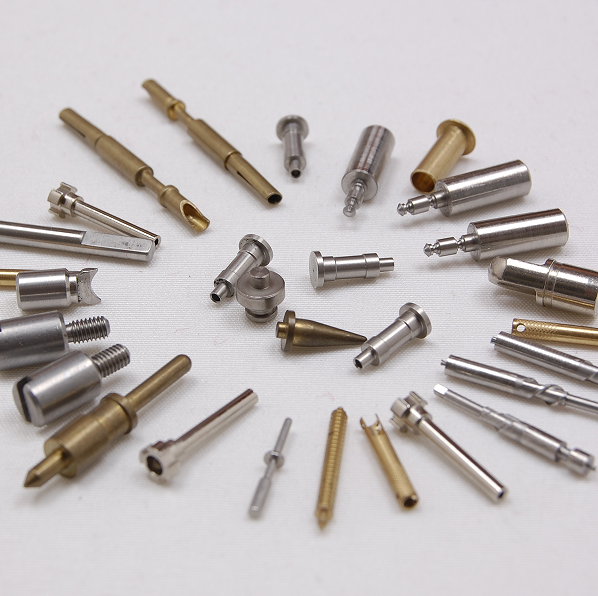
High-speed and high-precision machine tool thermal analysis and thermal design technology Source:
With the continuous advancement of related technologies such as design, manufacturing, assembly and materials of CNC machine tools and parts, the proportion of geometric errors, tool wear, servo and other errors in the overall errors of CNC machine tools is gradually decreasing. Under
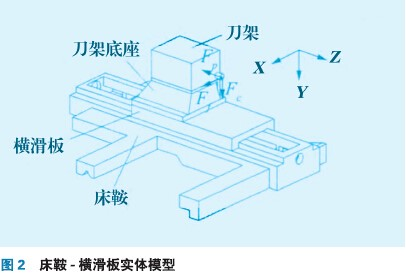
Performance analysis of slide rail connection surface based on machine tool stiffness introduction
In order to achieve certain motion functions of machine tools, the components are combined by connecting surfaces. The connection surface is divided into fixed connection surface (such as bolt connection), semi-fixed connection surface
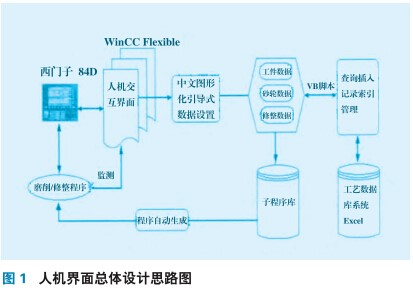
Application of WinCC+Flexible in CNC machine tool interface development
At present, Siemens CNC systems are increasingly widely used in my country's machine tool industry. The standard human-computer interaction interface of the Siemens 840D CNC system
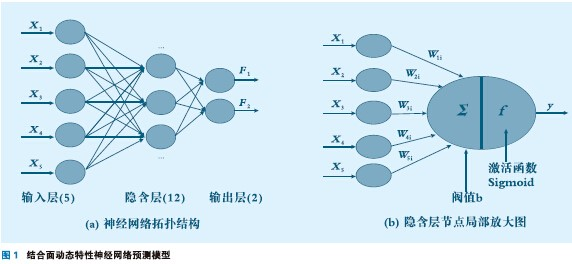
Modeling and simulation of dynamic characteristic parameters of joint surface of CNC machine tools
Since there are joint surfaces between machine tool components, the "flexible" nature of the joint surfaces that both stores and consumes energy greatly affects the static and dynamic characteristics of the entire machine tool. The stiffness and damping between the combined surfaces, especially the damping, are often greater than the elasticity and damping of the structure
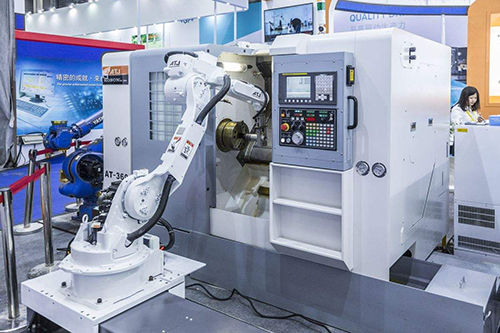
Analysis of dynamic characteristics of CNC machine tool spindle system
The CNC machine tool spindle system includes components such as spindle, bearings, tool holders, tools (or workpieces), etc., and is an important subsystem of CNC machine tools. The dynamic characteristics of the spindle system directly affect the machining accuracy, surface roughness and productivity of the workpiece. Therefore, the dynamic design and analysis of the spindle system has attracted widespread attention from the business community and scholars. In particular, in recent years, the d
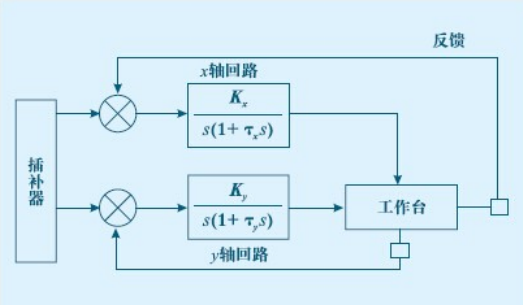
Precision analysis and control research on machine tool feed system
The feed system of CNC machine tools is mainly the servo feed method of servo motor + ball screw. The rotary motion output by the servo motor is converted into linear motion of the controlled object through a series of intermediate transmission devices such as couplings and ball screw pairs. The structural block diagram of its mechanical system is shown in Figure 1, and the mathematical model is:
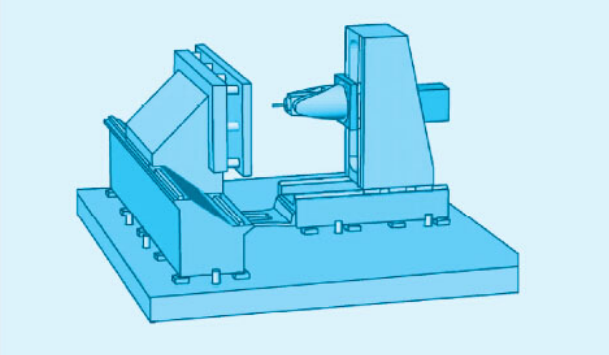
Research on spatial error modeling of universal spindle head of five-axis CNC machine tools
With the extensive application of free-form surfaces, modern manufacturing industry has an increasing demand for five-axis machine tools. Five-axis machine tools can be divided into several types according to different structures: double turntable type, turntable plus swing axis type, universal spindle head type, etc. The two rotary axes of the universal spindle head type CNC machine tool are both located on the spindle. Since the universal spindle head adds two rotating axes compared to other t